塑料薄膜印刷中套印不准的深度解析
日期:2024-10-23 22:18
在塑料薄膜的凹版印刷过程中,有多种故障类型,其中套印不准是常见的一个问题。这种问题不仅影响印刷质量,还可能导致材料的浪费,因此引起了业内人士的高度关注。了解造成套印不准的原因,并掌握解决方法显得十分必要。本文结合笔者多年来在凹版印刷领域的经验,对套印不准进行了分析,希望能为业界提供参考。
塑料薄膜的凹版印刷流程是:承印物通过放料装置进入第一单元进行印刷,随后经过烘干装置,再在传导辊的帮助下进入第二单元印刷,以此类推,最后进入收卷装置。在这一过程中,为避免因套印不准造成损失,必须确保放卷与收卷时的张力一致,同时还要关注套印不准的趋势,并采取相应的解决措施。
套印不准的原因主要有多方面,包括机械设备的性能、油墨的适应性、环境温度等客观因素,也涉及到操作人员的质量意识等主观因素。以下将对这些因素进行逐一详细分析。
一、卷筒直径的影响因素
料卷直径越大,塑料在运行中越容易偏移,可能导致套印不准确。根据经验,选择合适的料卷直径是非常重要的。在印刷过程中,随着料卷直径的逐渐减小,需相应降低放卷张力,以确保料张力保持稳定。这可以通过手动齿轮或磁粉制动器来调节。在操作时,要注意观察印刷的色标是否出现走样。
在35-40cra的国产多色凹印机中,版滚筒的轴向定位是依靠滚筒端的U型槽与机架上的轴承之间的配合。轴承厚度与U型槽宽度相匹配,但如果U型槽磨损导致宽度增加,版轴可能会引起版滚筒的轴向窜动,从而影响套印的准确性。当磨损量超过0.3mm时,套印的不准确和图案走样将变得十分明显。作为操作者,应定期在凹印机的滑动部件和齿轮等运动部位添加机油,以确保套印的精准,并延长机械寿命、减少磨损。当出现明显磨损时,应更换损坏的部件。一旦版轴发生轴向窜动,承印物上的色样也会变得不稳定,色标会出现位移。
二、导辊带电
在印刷过程中,塑料薄膜需要通过导辊的牵引进入下一个印刷单元或烘干设备。然而,塑料薄膜与导辊之间的摩擦会导致导辊产生静电,吸附空气中的灰尘,造成导辊局部变脏,这可能导致薄膜在轴向上的滑动,从而影响套印的精度。因此,在停机时,应对导辊进行清洁,以为下次印刷做好充分准备。
三、装版不当
套印不准确与装版密切相关。在进行装版之前,首先应将版轴彻底清洁,然后将印版准确地安装在轴的中心位置。印版两端的堵头(也称为闷头)需平整装配,锁版时要均匀用力,以确保套印的准确性。一般情况下,版轴的配合间隙应保持在0.04-0.06mm,当间隙达到0.2mm时,套色会变得困难;如果间隙达到0.4-0.6mm,则需要进行更换。由于长期运转,印刷单元的齿轮会经历不同程度的磨损。如果版滚筒齿轮与主传动轴上的齿轮未在分度圆处对齐,转速会出现不稳定,导致精度下降,从而影响套印的准确性。这种情况通常表现为承印物上的色标出现上下偏移且不稳定。
四、胶辊选择不当。
为了获得更高的套准精度,胶辊的选择必须非常谨慎。我厂曾遇到一次套印不准的问题,通过更换材料、重新检测印版和调整张力,仍未能获得理想效果。后来的检查发现,一条橡胶压辊的两端直径相差0.015mm,经过更换新的压辊后问题得到解决。通常,在印刷厚度为12微米的宽幅薄膜时,对胶辊的要求更加严格。此外,还需确保压辊与印版之间的压力均匀,否则也会导致套印不准确等问题。胶辊压力不均和塑料薄膜厚度不一致都会直接影响套印精度,一般表现为图像的横向偏移。在印刷过程中,最后一个单元与第一个单元相比,薄膜会因温度变化而伸缩,从而造成套印不准。因此,在印刷时,应尽量使溶剂有效挥发,并保持较低的烘干温度。同时,印刷环境的温度和湿度也需严格控制,建议车间内温度保持在25℃、湿度控制在40%左右。过高或过低都会影响套印精度。此外,油墨的黏度过大也会引起图像位移,因此黏度值应根据实际情况进行调整。
五,印版递增量
在凹版印刷过程中,需考虑塑料薄膜的拉伸情况,并根据色序调整印版的递增量,这一递增量是逐步增大的。如果递增量出现误差,超出允许范围,套色的准确性也会受到影响。因此,在印版滚筒投入使用前,需要仔细检查并记录相关数据,印刷时也要认真对比印件与原稿。
六、收卷张力
在塑料薄膜的生产过程中,收卷张力需要保持稳定。随着收卷直径的逐渐增加,收卷张力也应相应上升。此外,要关注收卷过程中的抖动范围,因为收卷张力是通过收卷轴端摩擦滚动轴承上的摩擦片进行调整。如果抖动幅度过大,薄膜会出现收缩,导致张力增高。通常,可以通过磁粉制动器或手动调节来控制张力。还需注意的是,卷材越长,越容易被拉伸,因此张力值也需相应调整,保持恒定而平稳的张力非常重要。总之,要获得准确的套印和优质的塑料薄膜印刷品,必须妥善处理每一个工序,并认真分析问题,总结经验,为未来提供借鉴。
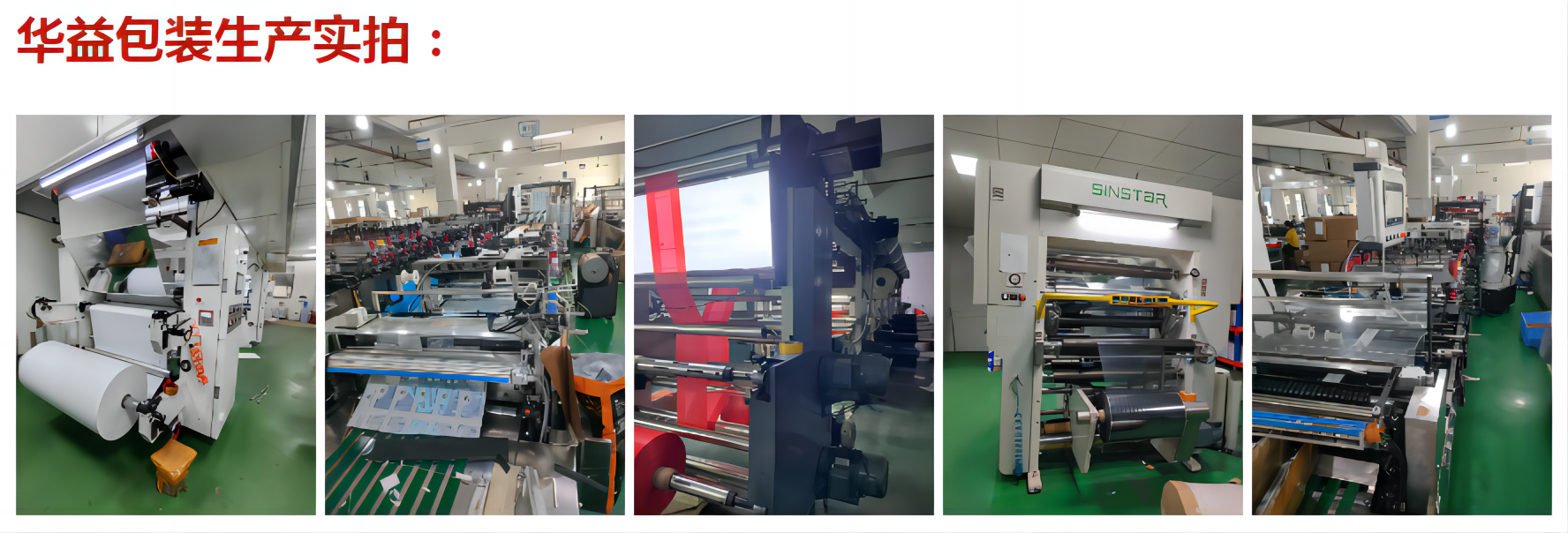
文章编辑:华益塑料包装袋印刷厂家
更多软包装信息请登陆:https://www.vipzai.com 欢迎联系与咨询我们!我们将为您提供全方位的、优质的产品和服务....
塑料薄膜的凹版印刷流程是:承印物通过放料装置进入第一单元进行印刷,随后经过烘干装置,再在传导辊的帮助下进入第二单元印刷,以此类推,最后进入收卷装置。在这一过程中,为避免因套印不准造成损失,必须确保放卷与收卷时的张力一致,同时还要关注套印不准的趋势,并采取相应的解决措施。
套印不准的原因主要有多方面,包括机械设备的性能、油墨的适应性、环境温度等客观因素,也涉及到操作人员的质量意识等主观因素。以下将对这些因素进行逐一详细分析。
一、卷筒直径的影响因素
料卷直径越大,塑料在运行中越容易偏移,可能导致套印不准确。根据经验,选择合适的料卷直径是非常重要的。在印刷过程中,随着料卷直径的逐渐减小,需相应降低放卷张力,以确保料张力保持稳定。这可以通过手动齿轮或磁粉制动器来调节。在操作时,要注意观察印刷的色标是否出现走样。
在35-40cra的国产多色凹印机中,版滚筒的轴向定位是依靠滚筒端的U型槽与机架上的轴承之间的配合。轴承厚度与U型槽宽度相匹配,但如果U型槽磨损导致宽度增加,版轴可能会引起版滚筒的轴向窜动,从而影响套印的准确性。当磨损量超过0.3mm时,套印的不准确和图案走样将变得十分明显。作为操作者,应定期在凹印机的滑动部件和齿轮等运动部位添加机油,以确保套印的精准,并延长机械寿命、减少磨损。当出现明显磨损时,应更换损坏的部件。一旦版轴发生轴向窜动,承印物上的色样也会变得不稳定,色标会出现位移。
二、导辊带电
在印刷过程中,塑料薄膜需要通过导辊的牵引进入下一个印刷单元或烘干设备。然而,塑料薄膜与导辊之间的摩擦会导致导辊产生静电,吸附空气中的灰尘,造成导辊局部变脏,这可能导致薄膜在轴向上的滑动,从而影响套印的精度。因此,在停机时,应对导辊进行清洁,以为下次印刷做好充分准备。
三、装版不当
套印不准确与装版密切相关。在进行装版之前,首先应将版轴彻底清洁,然后将印版准确地安装在轴的中心位置。印版两端的堵头(也称为闷头)需平整装配,锁版时要均匀用力,以确保套印的准确性。一般情况下,版轴的配合间隙应保持在0.04-0.06mm,当间隙达到0.2mm时,套色会变得困难;如果间隙达到0.4-0.6mm,则需要进行更换。由于长期运转,印刷单元的齿轮会经历不同程度的磨损。如果版滚筒齿轮与主传动轴上的齿轮未在分度圆处对齐,转速会出现不稳定,导致精度下降,从而影响套印的准确性。这种情况通常表现为承印物上的色标出现上下偏移且不稳定。
四、胶辊选择不当。
为了获得更高的套准精度,胶辊的选择必须非常谨慎。我厂曾遇到一次套印不准的问题,通过更换材料、重新检测印版和调整张力,仍未能获得理想效果。后来的检查发现,一条橡胶压辊的两端直径相差0.015mm,经过更换新的压辊后问题得到解决。通常,在印刷厚度为12微米的宽幅薄膜时,对胶辊的要求更加严格。此外,还需确保压辊与印版之间的压力均匀,否则也会导致套印不准确等问题。胶辊压力不均和塑料薄膜厚度不一致都会直接影响套印精度,一般表现为图像的横向偏移。在印刷过程中,最后一个单元与第一个单元相比,薄膜会因温度变化而伸缩,从而造成套印不准。因此,在印刷时,应尽量使溶剂有效挥发,并保持较低的烘干温度。同时,印刷环境的温度和湿度也需严格控制,建议车间内温度保持在25℃、湿度控制在40%左右。过高或过低都会影响套印精度。此外,油墨的黏度过大也会引起图像位移,因此黏度值应根据实际情况进行调整。
五,印版递增量
在凹版印刷过程中,需考虑塑料薄膜的拉伸情况,并根据色序调整印版的递增量,这一递增量是逐步增大的。如果递增量出现误差,超出允许范围,套色的准确性也会受到影响。因此,在印版滚筒投入使用前,需要仔细检查并记录相关数据,印刷时也要认真对比印件与原稿。
六、收卷张力
在塑料薄膜的生产过程中,收卷张力需要保持稳定。随着收卷直径的逐渐增加,收卷张力也应相应上升。此外,要关注收卷过程中的抖动范围,因为收卷张力是通过收卷轴端摩擦滚动轴承上的摩擦片进行调整。如果抖动幅度过大,薄膜会出现收缩,导致张力增高。通常,可以通过磁粉制动器或手动调节来控制张力。还需注意的是,卷材越长,越容易被拉伸,因此张力值也需相应调整,保持恒定而平稳的张力非常重要。总之,要获得准确的套印和优质的塑料薄膜印刷品,必须妥善处理每一个工序,并认真分析问题,总结经验,为未来提供借鉴。
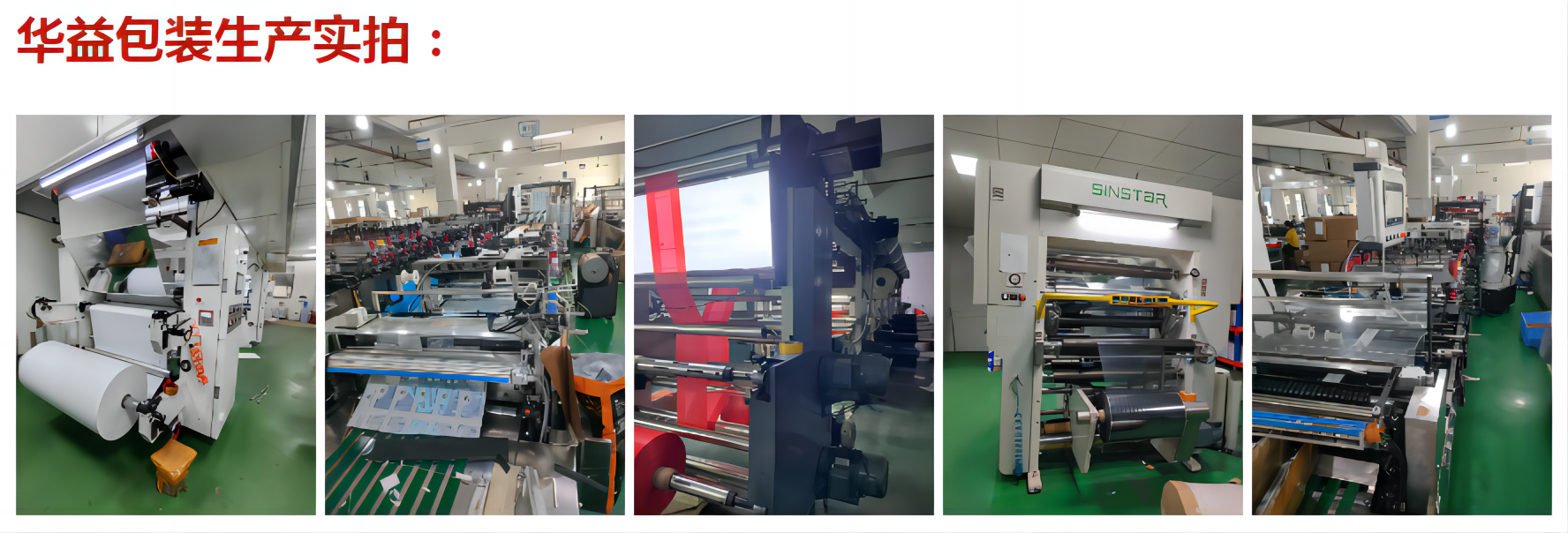
文章编辑:华益塑料包装袋印刷厂家
更多软包装信息请登陆:https://www.vipzai.com 欢迎联系与咨询我们!我们将为您提供全方位的、优质的产品和服务....